Comprehensive Guide: What is Porosity in Welding and Just How to stop It
Comprehensive Guide: What is Porosity in Welding and Just How to stop It
Blog Article
Porosity in Welding: Identifying Common Issues and Implementing Best Practices for Avoidance
Porosity in welding is a prevalent concern that frequently goes undetected up until it causes substantial issues with the stability of welds. In this conversation, we will certainly explore the vital aspects adding to porosity development, examine its detrimental impacts on weld efficiency, and review the finest methods that can be embraced to minimize porosity incident in welding processes.
Common Sources Of Porosity

Another frequent wrongdoer behind porosity is the existence of contaminants on the surface area of the base steel, such as oil, oil, or rust. When these pollutants are not properly gotten rid of prior to welding, they can evaporate and end up being trapped in the weld, triggering problems. Utilizing dirty or damp filler products can present pollutants right into the weld, contributing to porosity issues. To mitigate these typical reasons for porosity, thorough cleansing of base metals, proper protecting gas selection, and adherence to optimum welding specifications are essential techniques in attaining high-grade, porosity-free welds.
Influence of Porosity on Weld Quality

The presence of porosity in welding can considerably jeopardize the architectural honesty and mechanical buildings of bonded joints. Porosity creates spaces within the weld steel, weakening its general stamina and load-bearing ability.
Welds with high porosity levels have a tendency to show reduced influence strength and minimized capability to warp plastically before fracturing. Porosity can impede the weld's capability to successfully transfer forces, leading to early weld failure and potential safety and security dangers in vital More hints structures.
Ideal Practices for Porosity Avoidance
To enhance the structural honesty and quality of welded joints, what details procedures can be implemented to lessen the incident of porosity during the welding process? Making use of the proper welding method for the particular product being welded, such as adjusting the welding angle and weapon setting, can even more avoid porosity. Routine examination of welds and prompt remediation of any type i was reading this of issues determined during the welding procedure are crucial techniques to stop porosity and generate high-quality welds.
Significance of Proper Welding Methods
Applying appropriate welding techniques is critical in making sure the structural stability and quality of welded joints, developing upon the structure of effective porosity prevention procedures. Extreme warm can lead to increased porosity due to the entrapment of gases in the weld pool. Furthermore, making use of the suitable welding criteria, such as voltage, current, and travel rate, is crucial for achieving sound welds with very little porosity.
In addition, the choice of welding process, whether it be MIG, TIG, or stick welding, need to align with the certain demands of the project to guarantee optimum outcomes. Appropriate cleaning and prep work of the base metal, along with choosing the ideal filler product, are likewise crucial parts of skillful welding strategies. By sticking to these ideal methods, welders can reduce the danger of porosity development and produce premium, structurally audio welds.
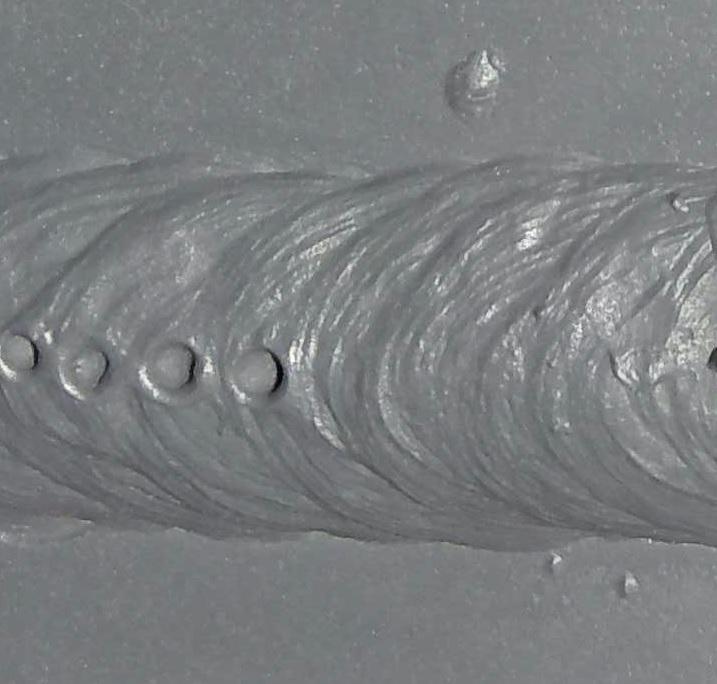
Testing and Quality Assurance Procedures
Evaluating treatments are important to detect and stop porosity in welding, making certain the strength and longevity of the final item. Non-destructive screening methods such as ultrasonic testing, radiographic screening, and aesthetic evaluation are generally used to identify possible flaws like porosity.
Performing pre-weld and post-weld inspections is likewise important in maintaining quality assurance criteria. Pre-weld examinations involve verifying the products, devices setups, and tidiness of the workplace to prevent contamination. Post-weld inspections, on the other hand, analyze the final weld for any kind of defects, consisting of porosity, and confirm that it satisfies defined criteria. Applying a detailed quality assurance strategy that includes comprehensive screening treatments useful content and evaluations is vital to decreasing porosity concerns and ensuring the overall quality of bonded joints.
Conclusion
To conclude, porosity in welding can be a common issue that impacts the quality of welds. By determining the typical reasons for porosity and carrying out best methods for avoidance, such as appropriate welding strategies and screening steps, welders can make sure high quality and trusted welds. It is vital to prioritize prevention approaches to decrease the incident of porosity and preserve the stability of bonded frameworks.
Report this page